Supporting Electrified Vehicles with Stable Supplies of Lithium
The Toyota Tsusho Group is involved in the production business of lithium carbonate and lithium hydroxide, which are used as raw materials including cathode materials in lithium-ion batteries, and is contributing to the realization of carbon neutrality through the spread of electrified vehicles.
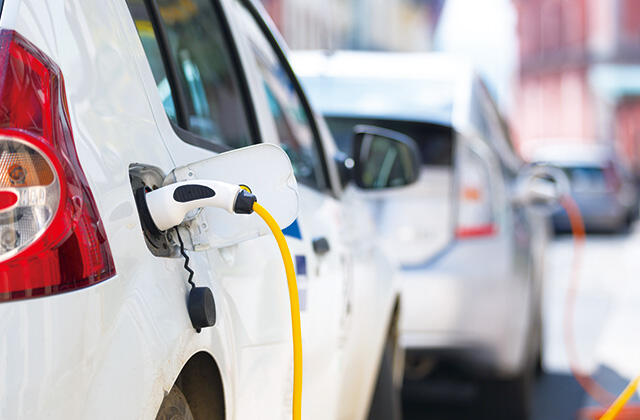
February 16, 2024
Project Background
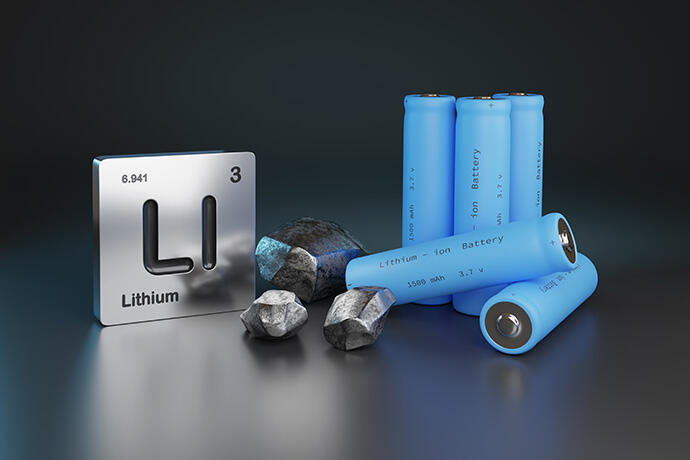
Lithium-ion batteries are used in smartphones, PCs, energy storage systems (ESS), and other technologies. It was around 2008 that Toyota Tsusho began investigating global mining reserves to acquire lithium in anticipation of increased demand associated with the spread of electrified vehicles.
Lithium is a type of rare metal produced in countries such as South America, Australia, and China. At the time, there were still few producers around the world, and Japan relied on imports for 100% of its lithium resources. As the spread of electrified vehicles is expected to accelerate, it was essential to develop new sources of supply to support the automobile industry.
There are mainly two types of lithium compounds used as raw materials for lithium-ion batteries. One is lithium carbonate (Li2CO3), which is produced by concentrating and refining salt lake brine (water containing salt) and ore extracted from mines. Apart from being used as a raw material for lithium-ion batteries, lithium carbonate is also used as a raw material for glass and ceramics, for example.
The other type is lithium hydroxide (LiOH), which is made by heating and reacting lithium carbonate and calcium hydroxide. Lithium hydroxide has many applications as a raw material for lithium-ion batteries, and cathode materials made from lithium hydroxide rather than lithium carbonate contribute to higher performance of lithium-ion batteries, such as higher energy density and superior charge-discharge characteristics.
Selected as a Development Partner
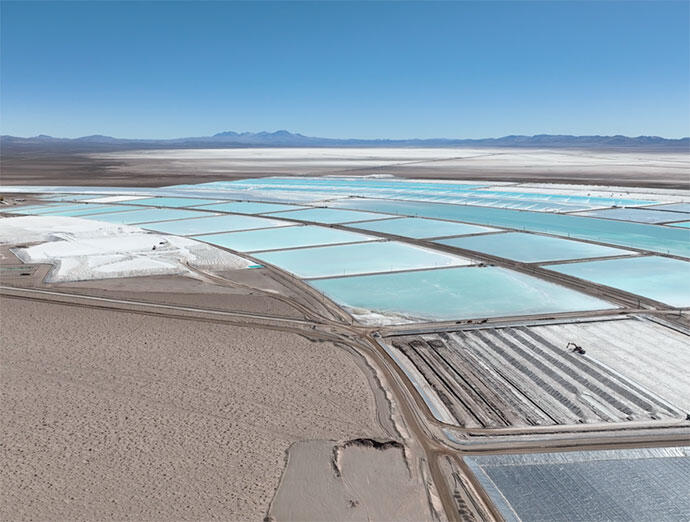
In 2008, Toyota Tsusho began to conduct studies on global mining reserves. The research led Toyota Tsusho to focus on Salar de Olaroz salt lake in Argentina. Although Salar de Olaroz was undeveloped, it is characterized by high levels of lithium in the brine with a low amount of impurities and offered an infrastructure needed for production and transportation.
In January 2010, as companies around the world were vying to secure mining rights to Salar de Olaroz, Orocobre Limited (currently Arcadium Lithium plc; hereinafter “Orocobre”), an Australian resources company with the rights to Salar de Olaroz, selected Toyota Tsusho as its development partner.
Toyota Tsusho was selected for being a member of the Toyota Group, which has sales routes on a global-scale, for being able to offer a complete upstream-to-downstream value chain, and for winning praise from Orocobre for its sustainable growth strategy.
Full-scale Production of Lithium Carbonate Begins
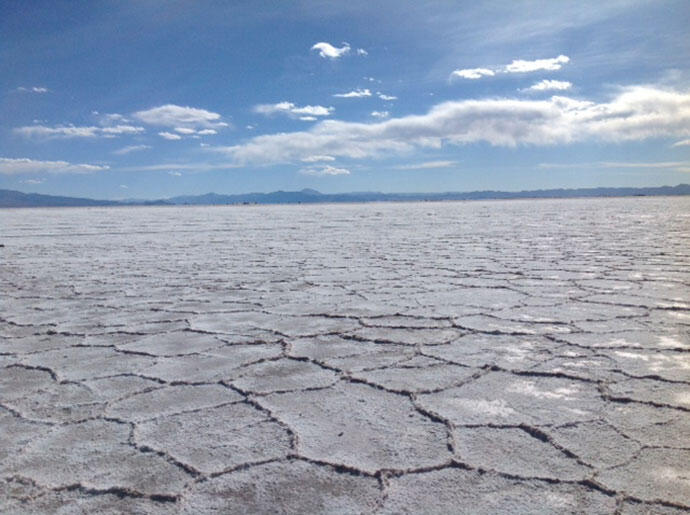
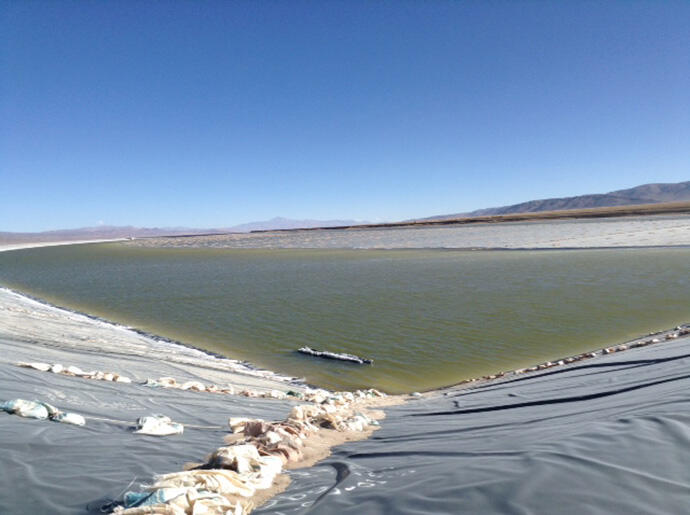
Toyota Tsusho and Orocobre (currently Arcadium Lithium plc) began joint feasibility studies, followed by the building of a pilot plant in 2011 to conduct demonstration tests. The Group acquired 100% of the sales rights and began providing the lithium carbonate produced at Salar de Olaroz to the market. In September 2012, Toyota Tsusho acquired a 25% stake in the project. In December of the same year, the partners began construction of a plant to draw brine from the salt lake and produce lithium carbonate.
The plant opened in December 2014, and commercial production finally began in 2015.
There are two main ways to produce lithium: refining it from brine and extracting it from crushed ore. This project uses the former, which employs fewer steps and costs less.
With few natural resources, Japan’s national strategy is to secure resources overseas. Since the Salar de Olaroz project is consistent with this strategy, Japan Organization for Metals and Energy Security (JOGMEC) has provided its full backing. JOGMEC provided technological support for mining reserve studies, undertook infrastructure feasibility studies, and offered debt guarantees.
Expanding Production to Meet Increased Demand
Production capacity was initially set at 17,500 tons/year, but due to expected growth in demand of automotive lithium-ion batteries, we decided to expand production capacity in November 2018. Specifically, we plan to construct additional wells to pump brine, evaporation ponds for concentration, and a refining plant. In 2023, we completed the construction of the second phase of plant equipment, which will increase production capacity from the current 17,500 tons/year to 42,500 tons/year. In the future, we will gradually increase production volume, aiming to reach a production capacity of 42,500 tons/year (completion of construction) by the end of 2024.
Production of Lithium Hydroxide for the First Time in Japan Begins
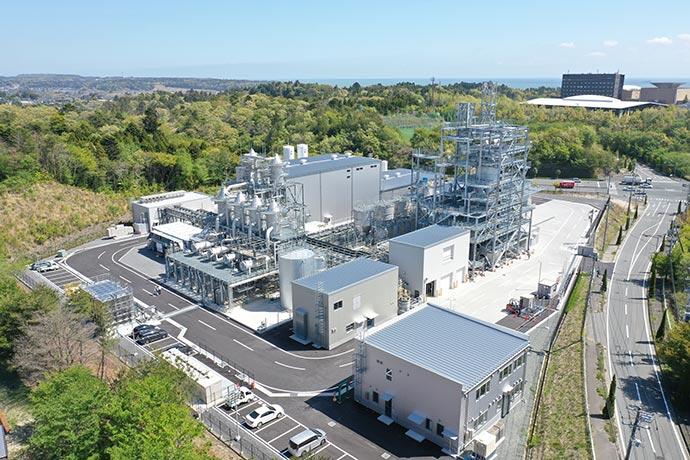
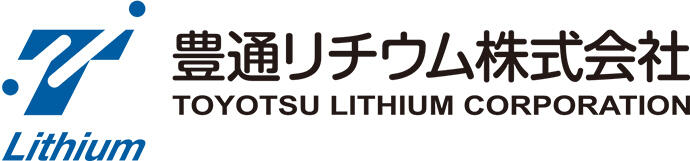
Location: 1-40 Nakamaru, Yamadaoka, Naraha-machi, Futaba-gun, Fukushima
Establishment: October 2018
Investment Ratio: Arcadium Lithium plc 75%, Toyota Tsusho 25%
(Voting rights ratio: Arcadium Lithium plc 49%, Toyota Tsusho 51%)
Even after lithium carbonate production began, electrified vehicles continued to spread rapidly, and the performance of automotive lithium-ion batteries continued to improve, leading to an increase in cruising distance.
Therefore, in 2018, Toyota Tsusho established Toyotsu Lithium Corporation as a group company and began the production of lithium hydroxide.
With an eye on sales domestically and to Asian countries such as South Korea, Toyota Tsusho constructed Japan’s first lithium hydroxide production plant in Naraha-machi, Fukushima Prefecture, close to demand areas.
The plant was completed on November 16, 2022. This project, based in Fukushima Prefecture, was eligible for the Subsidy Program for Industrial Location and Job Creation to Support Independence and a Return to Recovering Areas, from the Ministry of Economy, Trade and Industry and contributes to the revitalization of the local economy and the recovery of industries in the affected areas.
The production capacity of lithium hydroxide is 10,000 tons/year. The Group has acquired 100% of the sales rights and will sell the product to manufacturers in Japan and overseas, not only for use as raw materials for automotive lithium-ion batteries, but also for industrial applications. Since it is necessary to confirm that product quality meets demand and other factors, Toyota Tsusho is currently transitioning to a mass production system. Focusing on stable production and safe operation, Toyota Tsusho will expand production capacity and overseas operations in the future to meet the expectations of the rapidly growing lithium-ion battery market.
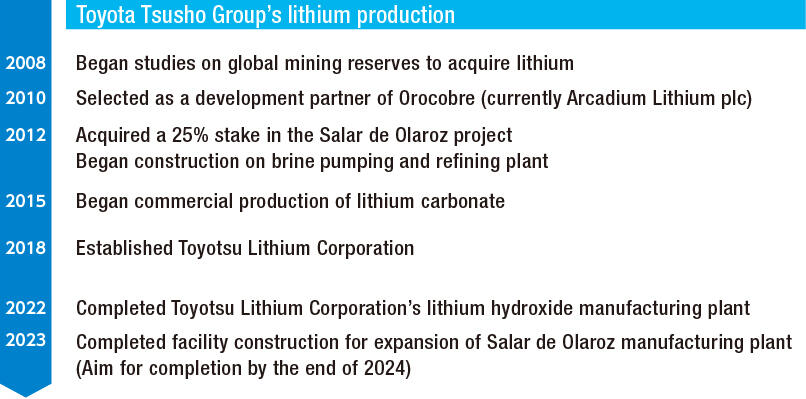
Realizing a Sustainable Society by Leveraging Our Strengths
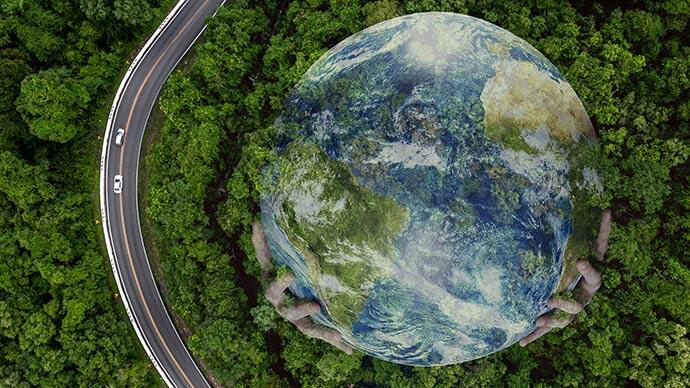
The Toyota Tsusho Group aims to enhance its business and corporate value by carrying out this project and contribute to the further development of downstream sectors by handling resources, which are the upstream sectors in the battery supply chain. In addition, as a new supplier in the lithium market, the Toyota Tsusho Group will support the spread of electrified vehicles and fulfill the mission “to pass down a better global environment to the children of the future” through carbon neutral initiatives.