Begin everything we do with ensuring safety and compliance, and continue to be an organization trusted by society
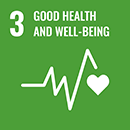
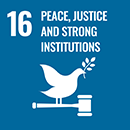
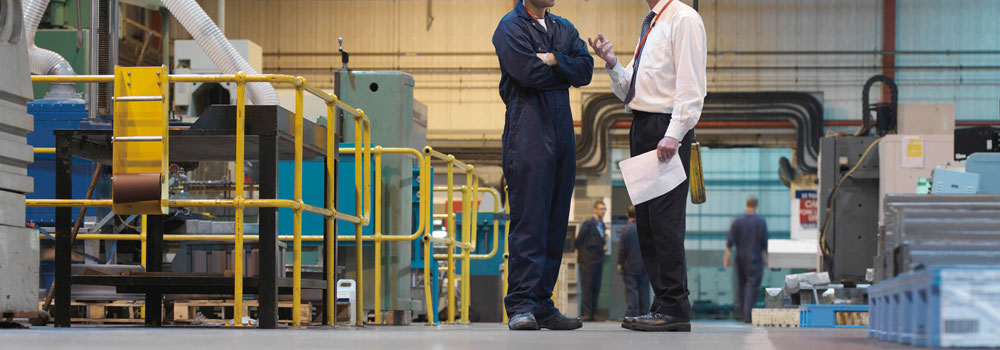
All corporate activities are supported by social trust and sustained by social confidence. Toyota Tsusho does its utmost to ensure safety at related companies and the safety of all workers. We are constantly engaged in activities that earn society’s trust and confidence, such as conducting safety education activities at plants and offices using our Practical Safety Workshop and ensuring high levels of quality that guarantee safety and (COCE) security.
In our day-to-day operations, we define specific codes of conduct for all sites and offices, both in Japan and overseas, and strictly comply with laws and regulations such as those concerned with preventing corruption or anticompetitive behavior. We are improving our management transparency and enhancing our corporate governance.
KPI
Lost work time incident rate*1, *2: Seeking zero accidents
Analysis of changes and actions taken
- Although there was a decrease compared to the fiscal year ending March 31, 2023, the ratio of accidents caused by inexperienced workers and accidents due to falls increased. The following countermeasures were thoroughly implemented:
- Continuation of follow-through activities, foreman training, and follow-up activities
- Continued education on 18 ironclad rules to prevent STOP6 incidents, which can lead to serious accidents
- Establishment of the 12 Insights for Preventing Falls and implementation of activities on a global scale
- *1The number of fatalities and injuries resulting from industrial accidents per million hours of actual work
- *2Scope: Main domestic and overseas affiliated companies
- *3Activities to eliminate recurrent accidents by identifying disaster themes (high-risk accidents, e.g., prevention of caught-in-between accidents, entrapment accidents, etc.) and implementing safety measures for them on a global basis
- *4Establishment of a support system at thae head office for business units that require intensive support
- *518 ironclad rules to prevent (STOP6) accidents (e.g., installing fences around the machinery that possibly cause accidents, a separation of path for pedestrian and vehicles)
- *6Six accidents that lead to possibly serious ones, including accidents caused by (1) moving machinery, (2) heavy objects, (3) contact with vehicles, (4) falls, (5) electric shock, and (6) high temperatures.
- Strengthening the quality of safety assurance and further improving systems
- Results
-
- Global implementation of fire and explosion prevention activities to maintain supply chains
- Company-wide implementation of e-learning and VR-based Office Safety Workshops to learn about office risks
- Construction safety supervision and factory inspections by management teams practicing an on-site, hands-on approach
- Promoting global compliance program
- Results
-
- Designation of October as compliance month each year, accompanied by messages from management and various training sessions and seminars to raise awareness
- Comprehensive compliance inspections at Toyota Tsusho and domestic and overseas consolidated subsidiaries
- Strengthening of the functions of the Board of Directors meeting
- Results
-
- Dialogue sessions between overseas regions (North America, East Asia, and Asia & Oceania) and outside directors to strengthen the supervisory function
- Strengthening the emergency response capabilities of the entire corporate group to deal flexibly with increasingly severe cyber attacks
- Results
-
- Continuous strengthening measures to prevent cyberattacks and conducting initial response drills based on a hypothetical cyber attack
Based on the beliefs that safety and compliance are the cornerstones for all work and that safety management is a matter of human resources development, Toyota Tsusho conducts safety and health education not just for Toyota Tsusho Group employees but, upon request, also for the employees of suppliers.
We conduct rank-based safety and health training for new employees, mid-level employees, managers, and executives and are expanding the scope of education by conducting training for persons involved in operations at suppliers.
To heighten employee sensitivity to danger by having them experience hazardous work, in 2009 we established a Practical Safety Workshop at Toyota Steel Center Co., Ltd. The workshop offers simulations of 62 different types of hazards, including being squeezed between objects and dangers involving heavy items. Educational materials on predicting six types of hazards have also been prepared. Workshop attendance is also open to the personnel of suppliers who take part in Toyota Tsusho’s Safety and Health Cooperation Council. The workshop serves to raise awareness regarding safety and health. Despite the effects of the COVID-19 pandemic, a total of 473 persons participated in these workshops in the fiscal year ended March 31, 2023, and the cumulative number of participants since their establishment reached 10,456 persons.
Taking into consideration that since Toyota Tsusho is a trading company and much of its work takes place in offices, in the fiscal year ended March 31, 2017, we began conducting Office Safety Workshops and taking measures to raise awareness of safety regarding office work. More than 900 participants from the Toyota Tsusho Group have attended these workshops to date.